The pressure on companies to reduce CO₂ emissions is ever increasing. At the same time, the price of coal and traded carbon will also keep rising into the future. These environmental and financial pressures will force all industries to review their energy and carbon positions. The use of alternative fuels has been recognized as a solution that can be adopted very quickly to mitigate the issue of CO₂ emissions.
However, the assumptions that it would require major plant modifications and would reduce the efficiency of daily operations have held companies back from moving to adopting alternative fuels.
In this blog, we tackle some of these misconceptions and explain how alternative fuels can seriously reduce CO2 emissions in major energy-consuming industries without affecting the continuity of your production process.
The cement industry: a frontrunner in reducing CO₂ emissions by using alternative fuels
As one of the biggest energy consumers in the world, the cement industry is finding innovative ways to reduce its environmental impact. The industry was an early adopter of alternative fuels technology, and the success of the cement sector should give other major energy-consuming industries comfort that adopting alternative fuel technology can be considered elsewhere and the know-how developed by the global cement sector can be applied in other industries.
In conclusion, the successful implementation of alternative fuels in the cement industry shows engineers in other industries that moving towards a more sustainable production process does not have to jeopardize their existing efficient internal processes. Indeed, the cement sector experience is that adopting alternative fuel technology can further enhance existing process efficiencies. Let's look at the most important insights based on the experience of the cement industry.
Numerous other stories circulate about the use of alternative fuels. Fortunately, these can all be refuted based on the latest findings. Read our trend report about the use of alternative fuels and discover all the myths and facts.
Achieve high levels of alternative fuel usage without compromising quality
Two main concerns existed when alternative fuels were first used in the cement industry, one was a subjective issue, and the second issue was more objective. The subjective issue was that the image of the finished cement product would be tarnished by the link with the use of waste-derived fuels.
This fear has proved to be misplaced. Indeed, the brand image of cement produced changed from being an environmentally negative product to one associated with the highest standards of environmentally sensitive recycling, so label cement made in this way as a ‘green’ product.
The objective concern is the management of trace metals, alkalis and chlorine in the finished product. Firstly, this concern has been managed by only using high-grade alternative fuels with low concentrations of trace metals, alkalis and chlorine. Secondly, changes to the cement kiln combustion process and quality management have also eliminated the concern regarding this issue.
Reduce CO₂ emissions without major modifications to your operations
The exact modifications needed will depend entirely on the existing plant, but a typical investment can be fairly modest. Return on investment for this type of capital spending has historically been very quick and, in the current climate, is even quicker due to the price of energy and CO₂.
Moreover, even old, out-of-date cement kilns have been used in the cement industry to burn alternative fuels. This demonstrates that a transition to alternative fuel is possible. For most types of kiln systems, that capital investment is not a limiting factor due to the rapid payback.
Identify bottlenecks, increase alternative fuel consumption, and to accurately target any required capital investment
All in all, implementing alternative fuels does not have to be as impactful and disruptive as it may seem. Finding and addressing any bottlenecks in advance of burning any alternative fuel , however, is an essential exercise when approaching a period of change, whether large or small scale. It can result in greater efficiency, possibly increased production, and an increased ability to burn higher levels of alternative fuels.
Therefore, conducting a plant audit relating to the burning of alternative fuels before changing the combustion system to burning alternative fuels is a sensible first step for any plant.
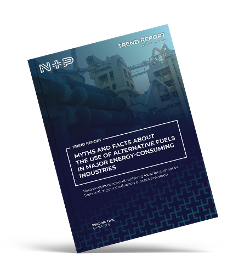
Interested in what such a plant audit looks like and which facets within your production process require special attention? Download our trend report "Myths and facts about the use of alternative fuels" and discover the most-common bottlenecks in production facilities.